Spline Rolling Process
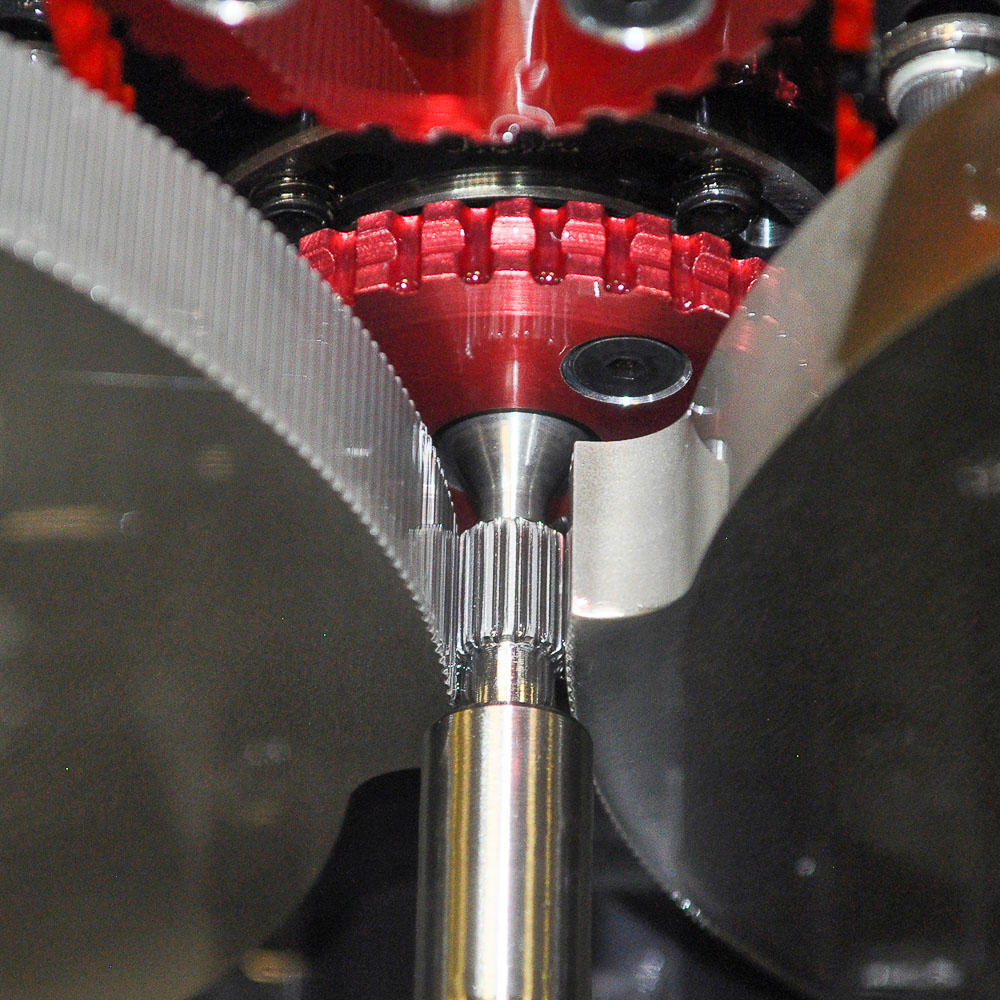
Spline Rolling & Serration Rolling
Kinefac spline and serration rolling processes are based on more than 60 years of innovation and experience in cylindrical die rolling. Unlike the rack rolling process where two opposing flat racks roll the form, Kinefac processes use two or three cylindrical dies which are driven in precise rotational phase to roll the form.
Splines and serrations are typically used in torque transmitting applications requiring a precision fit to a mating part as opposed to knurls which generally do not require a precision mating fit. Half shafts, drive shafts, electric vehicle motor shafts, and power take-off shafts are common types of splined and serrated components.
Splines and serrations on solid shafts can be rolled on Kinefac equipment using the infeed or single-revolution rolling process with two dies. In hollow shaft applications the forced-throughfeed rolling process with three dies can be used. The forced throughfeed rolling process can also be used to produce continuous lengths of splines and serrations on both solid and hollow shafts using two or three dies. Precision tolerance levels of ANSI Class 5 (DIN Class 8) or better can be achieved by Kinefac spline rolling processes.
Benefits of Spline Rolling
|
|
Spline & Serration Geometry
Spline and serration forms are described by an involute profile geometry with crest flat, root flat, pressure angle, and radius transitions at a fixed chordal pitch. Splines and serrations are either straight (parallel to the axis of the part) or have a lead (helix angle). Splines typically have pressure angles ranging from 20° to 37.5° while serrations typically have pressure angles ranging from 25° to 45°. ANSI B92.1 and B92.2M, ISO 4156, DIN 5480 and 5481, SAE J-500 and JIS specifications define industry standards for splines and serrations used around the world. The most important characteristics of splines and serrations are the measure-over-wire size and tooth spacing accuracy or index error.
Splines and serrations are generally classified by diametral pitch which is equal to the total number of teeth around the circumference divided by the pre-roll blank diameter, or by module which is equal to the pitch diameter in millimeters divided by the number of teeth. Splines and serrations up to 2.5 module with and without block teeth are rollable using the Kinefac cylindrical die rolling process depending on tolerance class, pressure angle, and tooth geometry.
Kinefac Spline Rolling Process
Key Requirements | Benefits |
---|---|
Stability, rigidity, and control accuracy of the rolling machine | Precise and repeatable pitch diameter and measure-over-wire |
Accuracy and precision of the spline rolling dies | Profile quality and good chordal tooth spacing |
Rotational synchronous accuracy of the spline rolling dies | Maintain die match with the work piece and tooth spacing accuracy |
Stability of the workpiece throughout the rolling process | Avoid tooth spacing error and runout |
Size of the pre-roll blank diameter | Achieve the correct number of teeth, chordal tooth spacing, and required fill of the spline major diameter |
Sufficient penetration speed of the spline rolling dies into the blank | Avoid over-fatigue and deep seams |
Sufficient dwell time when dies have reached their final penetration position | Roundness and form calibration |
Minimal friction between the workpiece and work support tooling | Prevent scuffing or other damage to the spline form during rolling |
Superior Spline Rolling for Demanding Applications
Transmission Shafts
Steering Shafts
Pump Shafts
Differential Case Shafts
Washer Shafts
Off Road Vehicle Comp.
Motorcycle Shafts
Agriculture Equipment
Truck Brake Systems
Automotive Drive Trains
Long Steering Splines
Drive Shafts
Air Compressor Shafts
Hollow Splines
Spline Rolling Process Control Features
POWERBOX machine structure
Kinefac 3-DIE machine structure with precision phasing plug
KINEFORM spline and serration rolling dies
True Die Position system
Auto-Assist Die Matching
Rotational position error monitoring with ultra-low backlash driveline
Flat blade, roller blade, bushing, and center support tooling
KineGlide low friction rolling blades
Servo blade automatic height control systems
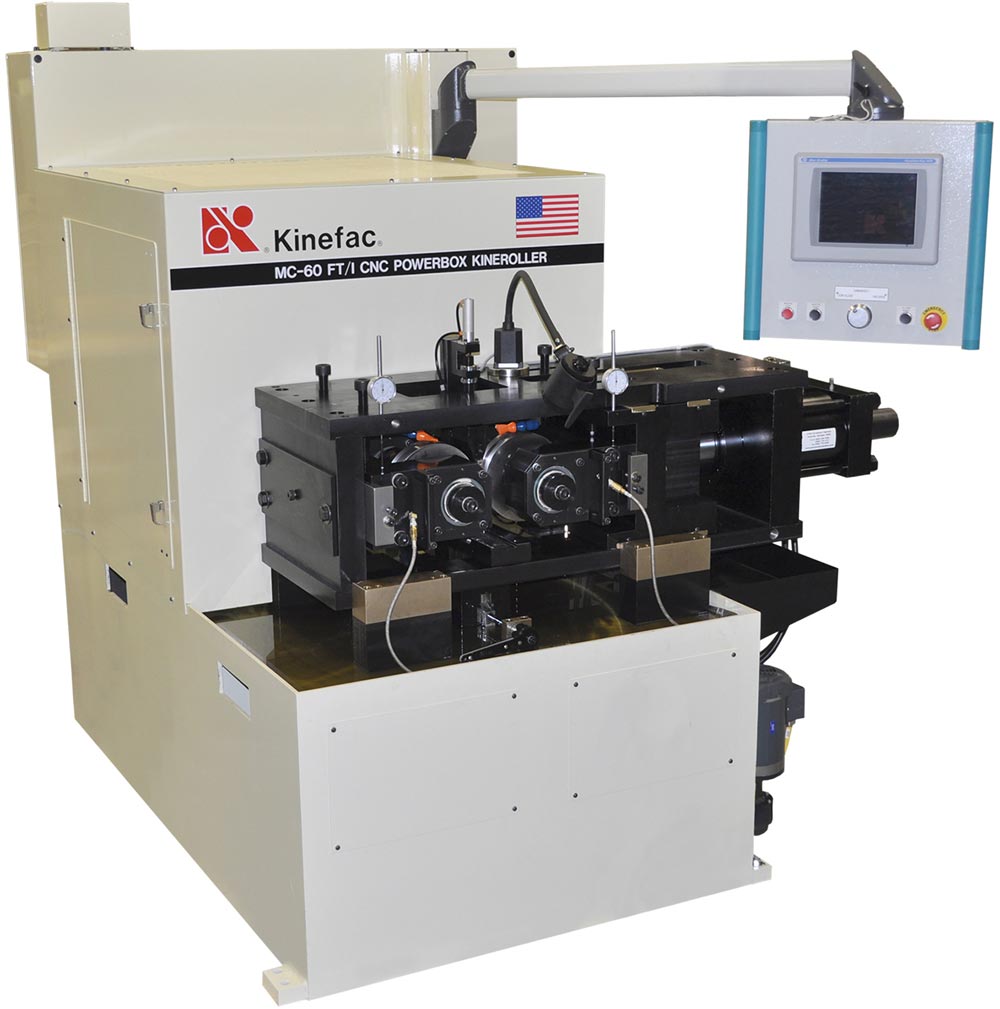
Spline Rolling Process Control Features
POWERBOX machine structure
Kinefac 3-DIE machine structure with precision phasing plug
KINEFORM spline and serration rolling dies
True Die Position system
Auto-Assist Die Matching
Rotational position error monitoring with ultra-low backlash driveline
Flat blade, roller blade, bushing, and center support tooling
KineGlide low friction rolling blades
Servo blade automatic height control systems
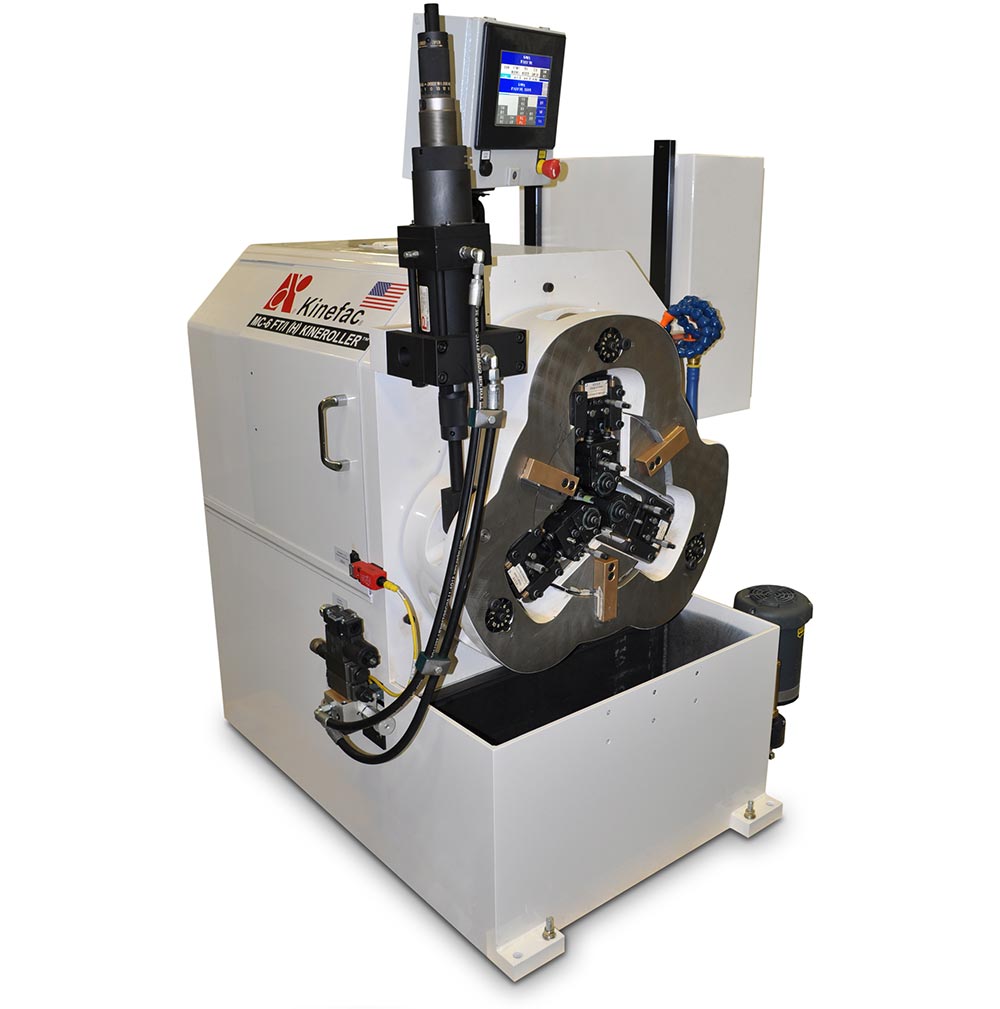