POWERBOX-PLUS™
POWER + PRECISION + VERSATILITY
Advanced CNC Performance
Kinefac offers a wide range of CNC Servo Technology to enhance the performance of your KineRoller. Depending on your application, our engineers will recommend one or a variety of features to meet your production needs while improving ease of setup.
“POWERBOX-PLUS” features have developed over decades of cylindrical die rolling experience. The Kinefac CNC Advanced Control System provides the user with full process control and improved rolling accuracy. Settings are easily made on the HMI touch screen which guides the operator through fault driven messaging. Programmed parameters can be saved and recalled for later use to greatly reduce setup time. The user-friendly interface and touch-button adjustment of CNC rolling also minimizes setup training needs.
- Recallable Part Program Creation by Menu-Driven Touch Buttons
- Automatic-Assist Die Matching
- Programmable Die Speed, Positions, Penetration Rates, and Dwell
- Variable Die Penetration Rates
- Controlled Reroll Cycles
- Die Force and Torque Monitoring with Die Saver Feature
- Interactive Fault Driven Operator Guidance
- Pre-Run Operator Setup Checklist
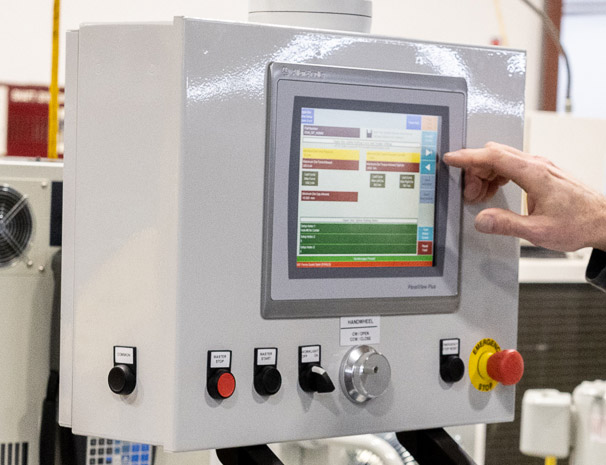
Our engineers are ready to help you design the right machine for your unique application.
Customize your KINEROLLER with our PLUS features designed for high precision rolling capabilities. Reduce setup time, improve rolled part consistency and quality, and reach new performance levels in rolling capability!
Available “PLUS” Enhancements
- Direct-Servo Spindle Drive
- Sensor Controlled Die Actuation
- True-Die Positioning System
- Smart Blade Rolling System
- Reciprocating Die Rolling
High Precision Direct Servo Drive (2 and 3 Die KineRoller)
The Kinefac direct drive servo system utilizes in-line zero-backlash planetary gearboxes directly connected to the machine spindles. The result is improved power transmission efficiency and improved angular positioning accuracy of the rolling dies.
Direct drive is well suited for spline and serration rolling applications where rotary phasing of the dies is critical for generating high quality forms with low spacing error. Fine independent rotary adjustments of the dies can be made on the machine HMI to achieve the optimum rolling conditions.
- Improved Tooth Spacing on Axial Forms
- Easy HMI fine adjustment for critical die phasing
- Responsive Die Rotation Control
- Variable Rotational Speed Control with RPM and Torque Balance
- Torque Monitoring
- Process Traceability
- Minimized Machine Footprint
Ultra-Low Backlash Servo Die Drive Systems with gearbox and low backlash universals are available for high torque applications such as high hardness aerospace, power generation, and automotive threaded fasteners.
Smart Sensor Controlled Servo Die Actuation (2 and 3 Die KineRoller)
Servo Die Actuation provides the user with HMI control of position, pressure, and die penetration speed with stored data features. Servo die actuation is well suited for high accuracy rolling applications where accurate and precise positioning of the dies is critical for maintaining pitch diameter and measurement over ball/pin dimensions.
Kinefac offers both servo electric and servo hydraulic die actuation system upgrades to provide the user with an increased level of precision die position control. Servo electric systems utilize roller screw technology for achieving high forces and precise positioning of the dies. Servo hydraulic system utilize servo proportional valve technology for achieving the necessary pressure, flow, and precise positioning of the dies. Both systems operate on closed loop feedback communication with and without linear transducers to ensure the commanded die position is met and maintained through the HMI.
- HMI Die Position Control
- Recall Stored Setup Data
- Programmable Go/No-Go Windows
- Force Monitoring and Penetration Speed Control
- Process Traceability
- Quick Setup Features
TRUE DIE POSITIONING SYSTEM
The highest accuracy rolling jobs such as precision ball screw and lead screw applications rely on more exact positioning of the dies to maintain repeatable pitch diameter or measurement over ball/pin dimensions. The Kinefac True Die Positioning System (TDP) combines the Smart Sensor Controlled Servo Die Closing System with position sensing probes in direct contact with the machine spindles which results in the most accurate die positioning feedback available! This system is designed to react to small runouts and changes in blank diameter or hardness while maintaining consistent commanded die position.
- Direct Contact Die Position Sensing
- Smart Closed-Loop Feedback
- Superior Pitch Diameter and MOW/MOB Control
- Die Saver Features
Smart Blade Rolling System
The standard Kinefac blade support system utilizes worm gear and cam technology to perform blade/tooling height settings and adjustments by manual operation. Upgrading to the Kinefac Smart Blade Rolling System allows the user to make simple height position adjustments through the HMI control.
Kinefac Smart Blade Rolling System utilizes closed-loop servo hydraulic or servo electric positioning with a linear position transducer. The user inputs the tooling height and desired rolling position below center to achieve automatic work height positioning without turning any adjustments. Blade height settings are saved in the HMI for future recall and minimized setup time.
Some materials such as titanium and stainless steel are sensitive to rolling on a blade when it comes to rolling a clean and fully formed thread crest. The Kinefac Smart Blade Rolling System can also be used to minimize the downward load applied to the work rest blade by controlling the blade height during the rolling process based on the radial growth of the thread. This action minimizes friction and helps to improve the rolled crest quality.
- Automatic Servo Blade Height Adjustment
- Fixed or Variable Centerline Rolling
- Minimization of Crest Flattening and Scuffing
- Quick Setup Features
RECIPROCATING DIE ROLLING (2 and 3 Die KineRoller)
The Kinefac High Precision Direct Servo Drive System allows for reciprocating die rolling capability. The rolling direction of the dies is automatically reversed back and forth during infeed penetration and dwell to control part feed and improve rolled form calibration.
Rolling applications such as splines, worms and other helical, axial, and annular forms can benefit from reciprocating rolling to improve formed tooth profiles and balanced seam formation.
- Automatic Reciprocating Die Rolling
- Part Feed Control
- Improved Rolled Form Calibration
- Uniform Seam Formation