FLUID EXTRACTION & RECOVERY
RECOVER VALUABLE MATERIALS FROM YOUR WASTE STREAM
KineSpin™ fluid extraction systems separate solid-liquid mixtures using centrifugal force.
THE SUPERIOR SOLID-LIQUID SEPARATION SOLUTION
Whether you need to separate contaminated fluids from chips for recycling and reuse, waste fluids from sludge or swarf, or aqueous fluids from chips to prepare surfaces for post operations – KineSpin fluid extracting solutions meet environmental requirements and maximize return on investment.
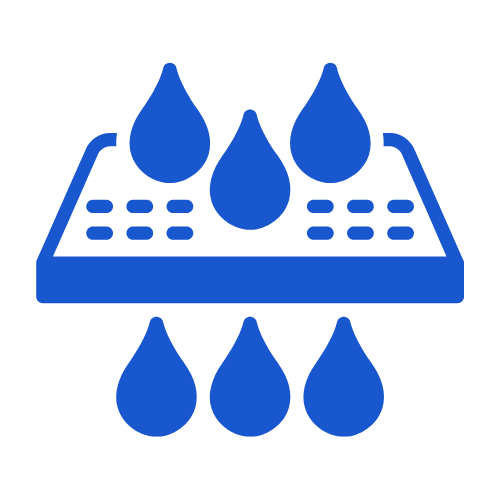
Reduce Disposal Costs
Reclaim oil and coolants for reuse to reduce annual fluid purchases.
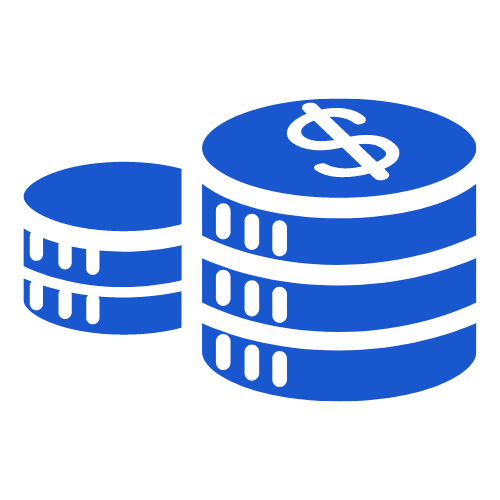
INCREASE SCRAP VALUE
Increase metal scrap value up to 20% with “dry” chips.
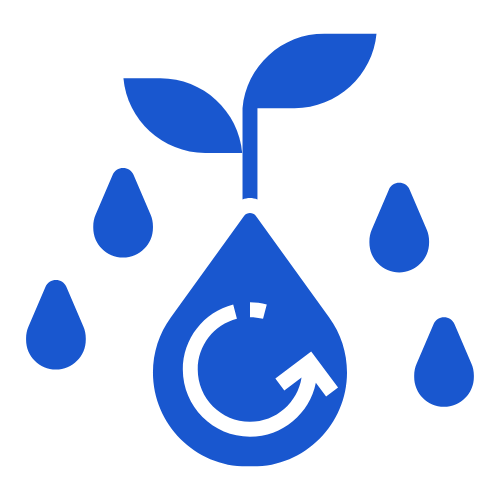
CUT CONTAMINATION LEVELS
Control fluid waste for easier disposal management.
DISCOVER KINESPIN FLUID EXTRACTION SYSTEMS
Custom Solutions for Industrial Fluid Extraction
KineSpin fluid extractors use centrifugal force to effectively extract all recoverable fluids from oily chips or turnings produced during machining, milling and turning operations. High centrifugal forces push the heavy solid particles toward the centrifuge pan wall. The displaced lighter liquid flows away from the solids through an outlet in the centrifuge pan/cover.
Centrifugal fluid extractors provide high separation efficiency, low maintenance costs, and maximum fluid recovery for reduced operating costs. Small enough to be placed in close proximity to the chip producing machine, the KineSpin fluid extractor is easily integrated with other equipment on the factory floor. Batch processing allows for easy chip separation and management.
Our Engineers Work With Customers On A Diverse Set of Custom Applications to Assure That We Meet Your Specific Needs
Chip Spinning (Wringing)
KineSpin fluid extractors spinning up to 400 G’s of centrifugal force wring fluids such as coolants and cutting oils from metal and plastic chips–removing up to 99% of fluids depending on material and application. In a batch process, pans of oily “wet” chips are placed in a rotating drum capable of rapid and high acceleration. The reclaimed fluids escape the pans and are discharged through an outlet into a capture tank to be reclaimed for future use. The “dry” and clean chips can be sold at a premium reducing operating costs.
Applications
- Cutting oil from metal chips and turnings
- Water soluble coolant from chips and turnings
- Oil or coolant from parts, stampings and headed parts
Before
After
Sludge/Swarf Extraction
The KineSpin fluid extractor is easily converted to a sludge extractor to handle your swarf extraction needs. Pans of sludge are secured in a rotating drum that is accelerated to high G’s causing solid particles to separate from the fluid slurry. The “dry” sludge accumulates on the inside wall of the pan while the free fluids escape over the pan wall. Removal of all free fluids by centrifugal force reduces the wet sludge to a dry cake with a moisture content of 5% to 15% depending on fluid and material. Cycle time is 15 to 20 minutes for water-based sludge and 30 to 45 minutes for oil-based sludge.
Applications
- Glass grinding
- Honing or metal grinding
- Quenching applications
- Cutting operations
Before
After
Washing & Drying
KineSpin fluid extractors can be customized to prepare contaminated industrial parts for subsequent surface finishing processes such as electropolishing or powder coating. During the wash cycle, an aqueous detergent is introduced into a pan containing the contaminated parts and spun at low RPM to agitate the parts in the wash solution. The RPM is then increased to discharge the solution back into the original capture tank. During the drying phase, air is circulated through an opening in the lid. The KineSpin wash-and-dry process uses less energy than conventional drying methods with low noise emission. An electric heater can be added to shorten cycle times.
Applications
- Preparation of metal parts for coating
- Washing and drying of non-metal parts such as glass or ceramic
- Recovery of clean high-value chips
- Washing of cold headed parts, fasteners, fittings